Astazi ne uitam la pulberi. Nu la parteneriatul cu Rheinmetall pentru fabrica de pulberi Victoria, instalatiile se vor pune in functiune – estimarea oficiala – peste 3 ani, daca nu vor fi si alte intarzieri, cum a fost procesul de expropriere.
Bineinteles ca vor exista si alte blocaje, asa ca speranta realista e ca fabrica sa fie pusa in functiune inainte de sfarsitul decadei. Pana atunci, actualul daunator de la Economie va fi de mult disparut din scaun, precum predecesorul, fara ca nimeni sa-l mai poata trage la raspundere.
Asa ca trebuie sa ne uitam la niste alternative.
De cateva zile circula o stire, preluata de internetzurile de specialitate asa, direct din comunicatul oficial al BAE:
BAE Systems has developed innovative new approaches in the production of energetics and propellants expected to strengthen supply chain resilience for the UK and its allies.
These developments follow more than £150m of investment by the Company in its UK munitions facilities since 2022, which will deliver a sixteen-fold increase in production capacity of 155mm artillery shells when its new explosive filling facility at Glascoed, South Wales, becomes operational this summer.
The Company has invested a further £8.5m in novel manufacturing methods over the last five years, leading to significant breakthroughs in the creation of next generation explosives and propellants. The new methods will use continuous flow processing to synthesise explosive material and remove the need for Nitrocellulose and Nitroglycerine, which are high in demand across global supply chains, in propellant production.
A pilot has already demonstrated the technological breakthrough producing the explosives in small nodes. This technology would remove the need for a large-scale explosive factory.
Atat. Nimic mai mult.
Pentru niste unii (nu spui cine) care nu mai au productie de nitroceluloza (NC) si nitroglicerina (NG) dar trebuie sa reia productia de pulberi urgent, nu sa astepte cel putin 3-4 ani dupa Rheinmetall, stirea de mai sus ar fi trebuit sa tina capul de afis si sa puna niste lucruri in miscare.
Aparitia unei tehnologii care elimina necesitatea unor fabrici de mari dimenisuni si permite dispersarea lor ar trebui sa fie din nou ceva foarte interesant pentru cei aflati foarte aproape de potentiala zona de conflict.
Si totusi curiozitatea pare sa fie la nivel minim. E adevarat, detaliile nu sint clare iar limbajul de marketing folosit amesteca explozivii cu pulberile astfel incat nu se intelege mare lucru fara a sapa mai adanc.
Din fericire, altii au sapat, de exemplu Business Insider:
A new formulation for propellants has been developed, it says, reducing the need for nitrocellulose and nitroglycerin, compounds that are in high demand across multiple industries worldwide.
At the same time, RDX explosives — the key explosive in 155 mm shells — are to be produced through continuous flow processing, a method that’s common in manufacturing but hasn’t yet been applied in defense.
It essentially means that shells are made in an uninterrupted process at a smaller scale rather than in large batches, an approach that, in other industries, has resulted in much greater efficiency.
The Times ofera si mai multe detalii:
Britain will dramatically increase its ability to produce explosives so it no longer needs to rely on the US and France for ammunition, The Times can reveal.
Shipping containers will be erected at sites across the UK to produce RDX explosives, used in 155mm rounds for British Army guns and other weapons.
BAE Systems, the UK defence company, is also looking to build three new sites to add “resilience” to the major project, in case one site comes under attack.
(…)
Steve Cardew, the business development director at BAE Systems’ Maritime and Land Defence Solutions, said: “The whole challenge for our industry is around production scale up and creating enough industrial capacity to effectively match Russia and other hostile nations.”
In an interview with The Times, he explained that RDX explosives used in 155mm rounds, mortars and warheads were normally developed in a relatively inefficient large-scale facility, however European nations were struggling to produce explosives at scale.
Under the plans outlined by BAE, each individual shipping container will produce up to 100 tonnes a year of explosives on a much smaller scale but one that is more efficient, cheaper and quicker. It is also more resilient in terms of security, he explained. “One large facility is clearly a big security threat. If you have dispersed facilities, it is much more secure.”
The innovative technology the firm has developed, using automation, has been proven as a concept and BAE now plans to manufacture its own explosives at scale. The system will then be sold to other countries so they can also produce their own sovereign explosives.
Vorbim deci despre doo lucruri distincte: pulberi de azvarlire fara NC/NG si exploziv RDX “produced through continuous flow processing“.
Interesant, procesul de productie al RDX corespunde foarte bine cu un patent al BAE Systems din 2020/2021 – Flow synthesis of RDX – care zice:
The use of flow synthesis provides a facile means of preparing RDX at both laboratory R&D scale of ˜100 g, and to provide the ability to add further flow reactors to readily scale up production, without the associated dangers of forming +100 Kgs of RDX explosive in a single reactor vessel. Further, it also avoids the use of hundreds of litres of highly concentrated acid in a large reactor vessel in a batch process. The use of flow synthesis allows for the continuous removal and safe stowage of final explosive product RDX material from the flow reactor or flow reactors, to avoid the build-up of large quantities of explosive material. This may allow explosive processing buildings to process a greater mass of explosive and/or associated safety distances to be reduced, as the explosive material may be distributed to safe areas, away from the flow reactor, as it is synthesised.
Noice…
In ceea ce priveste pulberile de azvarlire fara NC/NG, lucrurile sint mai complexe, existand putine surse publice care sa ne spuna exact cum si in ce fel, asa ca trebuiesc facute niste speculatii.
Tranzitia spre pulberi cu continut redus de NC/NG nu este un fenomen nou, existand chiar si o clasa intreaga de pulberi de acest fel numite LOVA (Low Vulnerability Ammunition), care elimina NG si reduc mult continutul de NC (sub 10%).
Britanicii sint cunoscuti pentru pulberea de mare energie destinata tunurilor de 120mm de pe tancuri – Rowanite 318 – compusa dintr-un polimer elastomeric EVA “umplut” cu exploziv (RDX sau, mai probabil, HMX – pentru ca monarhie) si NC undeva intre 5-10%.
Speculatia ar fi ca versiunea pentru obuzierele de 155mm ar elimina complet continutul de NC, in locul celei tripla baza clasice. Exista putine date publice care sa confirme asta, desi un patent mai vechi (2014) descrie niste compozitii care ar fi suspectii principali:
Este vorba deci de RDX sau HMX intr-o matrice polimerica EVA, cu plastificanti Butyl NENA si DOA. In plus, pentru a reduce sensibilitatea la diversi stimuli, este folosita nitroguanidina (picrita). Daca asta este compozitia-minune sau e vorba de ceva diferit, ramane de speculat.
Si toate astea pentru a scapa de dependenta fata de SUA… Ironia face ca singura fabrica americana de RDX (Holston Army Ammunition Plant) sa fie operata tot de BAE Systems – dar detinuta de guvernul SUA – asa ca la o prima vedere britanicii incearca sa scape de dependenta de ei insisi.
In realitate, guvernul SUA are ultimul cuvant asupra exporturilor de materiale sensibile, indiferent de cine opereaza fabrica, asa ca de fapt restrictiile ITAR ii mana in lupta pe britanici.
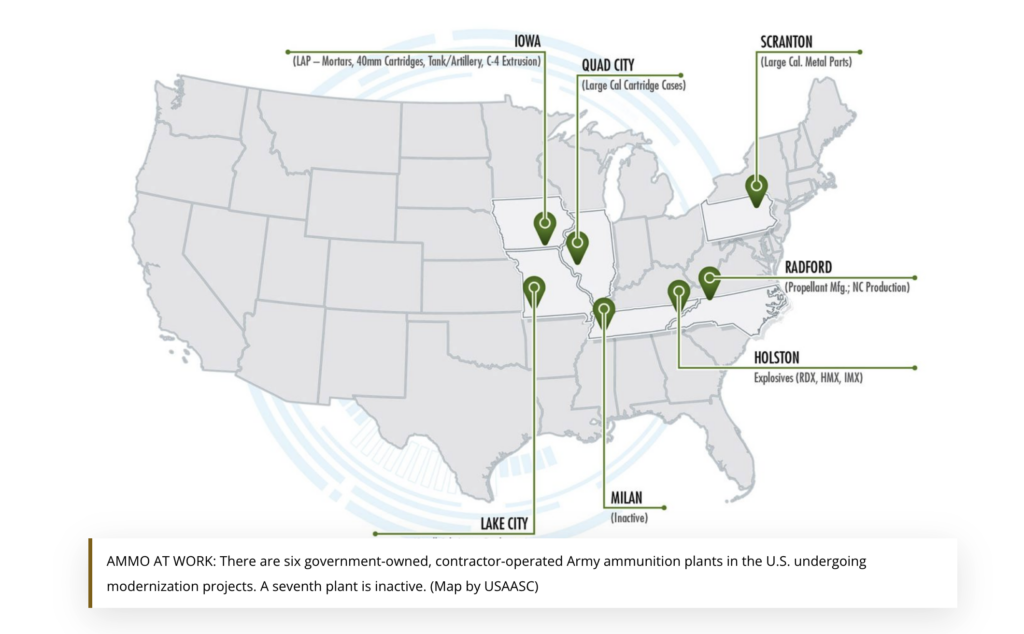
Si pentru ca am ajuns la fabricile din SUA ale BAE Systems, trebuie mentionata si cea de-a doua, Radford Army Ammunition Plant – care produce NC si pulberi de azvarlire – unde au aparut si sud-coreenii. Cum care, ii stiti, aia negri de respirau greu, Hanwha, cu care ne tot codim sa semnam un acord pentru modernizarea fabricilor noastre de pulberi.
Asta in cazul in care mai are sens dupa anuntarea parteneriatului cu Rheinmetall, poate pentru Fabrica de Pulberi Fagaras, care nu pare sa fie inclusa in planurile Rheinmetall.
Ei bine, coreenii de la Hanwha au fost contractati de BAE Systems pentru modernizarea Radford Army Ammunition Plant:
“BAE Systems is fully committed to modernizing the Radford Army Ammunition Plant and furthering its support of the U.S. Army’s requirements,” said John Swift, vice president and general manager of BAE Systems Ordnance Systems Inc. “We are excited to collaborate with Hanwha Defense USA, as they will use their proven expertise to help us integrate advanced chemical processing capabilities into a manufacturing environment.”
Modernization of World War II-era facilities is important for national security. (…)
“The upgrade is based on technology and experience that Hanwha has already completed in their Korean energetics facilities,” said John Kelly, president and CEO of HDUSA. “We look forward to implementing this upgrade at Radford and expanding our modernization collaboration with BAE Systems and the Army.”
E important deci de notat ca Radford Army Ammunition Plant a fost construita in anii ’40 si, desi unele instalatii sint in mod evident functionale, altele nu aratau inainte de modernizare foarte diferit de ruinele noastre de la Fagaras:

Unul din cei mai mari furnizori mondiali de explozivi nu are nici o problema sa dea un contract de modernizare catre Hanwha insa noi inca ne gandim, in loc sa semnam de urgenta, macar pentru Fagaras, cu conditia ca productia sa inceapa ieri.
Deci Hanwha nu ne trebuie (?), la fabricile-container ale BAE nici nu ne gandim, ce alternative raman pana cand Rheinmetall o sa construiasca fabrica mamut de la Victoria, care-e-vulnerabila-in-caz-de-ceva?
Sa incercam pe persoana fizica. Vestea buna e ca exista si asa ceva.
Proiectul „Încărcături de pulberi de azvârlire/propergoli solizi de mare energie obţinute prin fabricaţie aditivă – PropAM” este o soluţie inovativă pentru una dintre cele mai dificile probleme din domeniul balisticii: optimizarea ciclului balistic, controlul presiunii şi al temperaturii generate prin arderea pulberilor. Fiind conştientă de utilitatea practică a tehnologiei de imprimare 3D, echipa de proiect intenţionează să investigheze abilitatea tehnologiei FDM (Fused Deposition Modeling) de a produce pulberi de azvârlire pentru tunurile de calibru mare şi propergoli solizi pentru motoare-rachetă, fiabili şi eficienţi (TRL 3).
Ideea de baza de la care porneşte propunerea de proiect este exploatarea creativităţii nelimitate care este oferită de tehnologia de imprimare 3D în domeniul balisticii interioare. Mai exact, producerea de elemente de pulbere din unul sau mai mulţi constituenţi imprimabili care posedă viteze de ardere caracteristice diferite. Ideea proiectului este susţinută atât de munca şi opinia altor cercetători, cât şi de calculele preliminare şi conceptele dezvoltate în Academia Tehnică Militară “Ferdinand I”.
Daca fabricile-container ale BAE sint o solutie buna la problema scalarii productiei concomitent cu dispersia ei, atunci imprimarea 3D ar fi o solutie excelenta la aceeasi problema. Asta daca si performantele pulberilor vor fi similare.
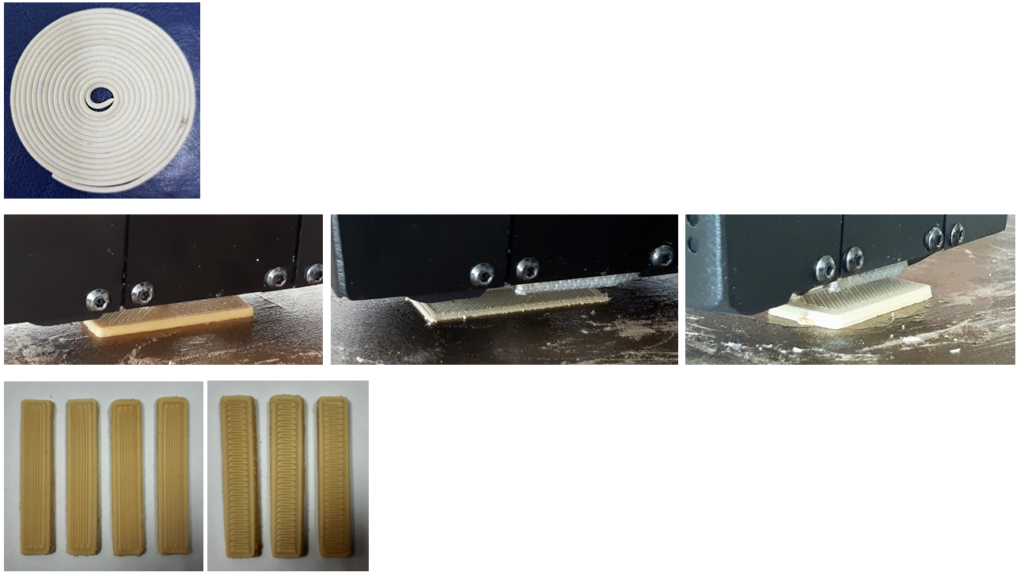
Cele trei raporte de etapa sint disponibile la sfarsitul postarii. Problema cu imprimarea 3D poate fi rezumata cam asa:
Fabricaţia aditivă prin tehnologia FDM este foarte puţin aplicată în obţinerea amestecurilor energetice deoarece procesul de imprimare presupune extrudarea termică a filamentelor formate din pulbere de înaltă energie şi materiale termoplastice. Din cauza faptului că tehnologia FDM necesită topirea materialului, numai anumite materiale energetice sunt compatibile cu procesul de extrudare, preponderent polimerii cu temperatură scăzută de topire. În general, materialele energetice sunt susceptibile la aprindere, deflagraţie sau detonaţie atunci când sunt supuse la forfecare şi frecare în timpul extrudării prin duză. Din acest motiv, punctul critic este reprezentat de controlul temperaturii de extrudare (atât în timpul procesului de extrudare a filamentului cât şi în timpul procesului de imprimare) care trebuie să atingă temperatura de topire a polimerului, dar care trebuie sa fie mai mică decât temperatura de decrepitaţie a materialului energetic oxidant.
Pe scurt, imprimarea 3D este compatibila doar cu anumite materiale, care la randul lor trebuie sa fie compatibile intre ele. Alegerea compozitiei este deci restrictionata, in comparatie cu fabricatia clasica, unde gama de selectie a materialelor este mai mare si deci exista mai multe posibilitati de a optimiza compozitia pentru performante maxime, fara constrangerile procesului de imprimare 3D.
Versiunea finală a compoziției chimice a materialului destinat imprimării se bazează pe utilizarea unui exploziv brizant EB (RDX) ca material energetic, cu o temperatură de auto-aprindere de 219 ºC, conform AOP-4491 “Energetic Materials Thermal Sensitivness and Explosiveness Tests”. Acesta este însoțit de un liant inert (LI), cu o temperatură maximă de topire de 110 ºC, și de un liant energetic (LE) stabil din punct de vedere termic până la temperaturi de aproximativ 170 ºC. Astfel, temperatura de imprimare a fost ajustată la 150 ºC pentru a corespunde temperaturii de curgere a amestecului obținut. Prin urmare, utilizarea acestei temperaturi permite desfășurarea procesului în condiții de siguranță, riscurile apariției unei reacții de aprindere sau explozie fiind extrem de redus.
Compozitia aleasa apare ca C4 in diagramele de mai jos, prima diagrama comparand pulberi de azvarlire iar cea de-a doua, combustibili racheta solizi.
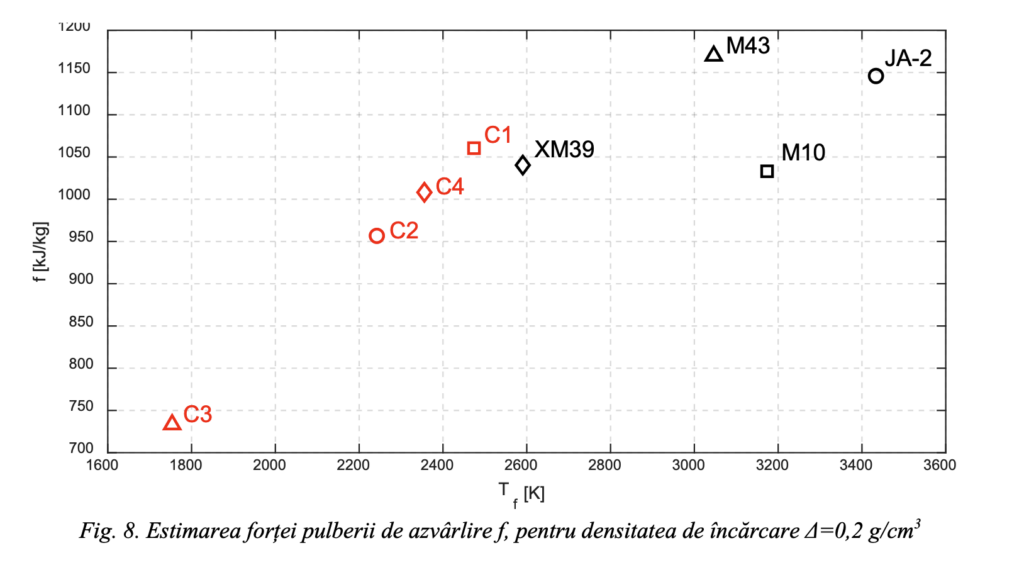
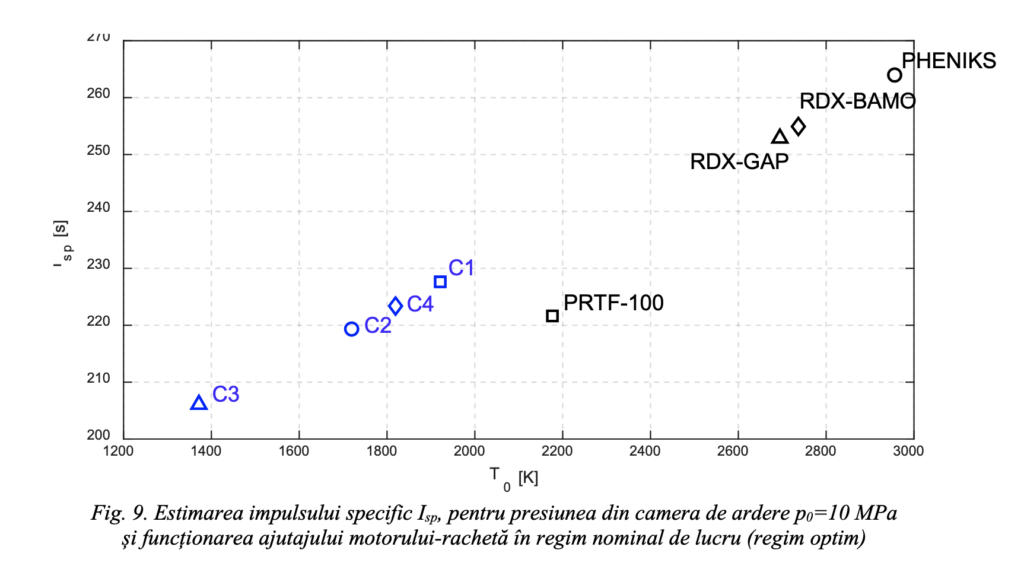
Vestea buna e ca s-a reusit obtinerea unei pulberi cu performante ce se apropie de XM39, pulberea LOVA “clasica”. La fel, in comparatie cu alti combustibili solizi, C4 este similara in performante cu pulberea omogena (dubla-baza) clasica PRTF-100.
Avand in vedere ca la momentul actual nu putem produce nici macar aceste pulberi clasice, alternativa C4 arata excelent. Calul de dar…
Vestea proasta este ca, evident, sintem departe de performantele-etalon de pe piata, a se vedea PHENIX de la Roxel. Sau altfel spus, (ca exemplu ipotetic) am putea reincepe productia de motoare pentru rachetele de 122mm cu performante similare celor clasice (~20km bataie maxima) dar pentru cele cu bataie extinsa (~40km bataie maxima) mai avem de cercetat. Sau sa continuam importul de la Roxel.
Avand in vedere ca proiectul era doar de nivel TRL 3, asteptarea era ca rezultatele sa se imbunatateasca, pe masura ce se vor incerca noi compozitii, in cazul in care se decidea continuarea lui. Ceea ce se pare ca s-a si intamplat – daca e adevarat, mare chestie pentru Romania – urmatoarea compozitie incercata fiind:
Notably, the formulation consisting of 70% RDX, 10% NC, and 20% polycaprolactone (PCL) emerged as the most advantageous option for gun propellants, owing to its exceptional processability, ease of printability, and high energetic performance.
Compozitia incepe sa semene cu o pulbere LOVA clasica dar formata prin imprimare 3D, observandu-se reintroducerea in compozitie a NC, cu dezavantajul necesitatii importului, pana la repunerea in functiune a productiei locale. Cu cuvintele lor:
The cyclotrimethylenetrinitramine/hexogen (RDX, 1.82 g/cm3 crystal density, melting point >200 C, purity >95%), conforming to MIL-DTL-398D, type I, class I, was acquired from energetic materials factory “Fabrica de pulberi Fagaraș” Romania as unphlegmatized crystals (15wt% water content). The nitrocellulose (NC, white fibrous solid, 12.6% nitrogen content, autoignition temperature >180 C, 30 wt% butanol content) was acquired from “Milan Blagojevic-Namenska” energetic materials factory, Serbia. The poly-caprolactone (PCL, z3 mm beads, 99.5% purity, average molecular weight Mn ¼ 80000 Da, 1.145 g/cm3 density) was purchased from Sigma Aldrich. The solvents: dichloromethane (DCM, 1.3 g/cm3 density, 99.5% min. purity), acetonitrile (ACN, 0.79 g/cm3 density, 99.5% min. purity), and n-Hexane (0.66 g/cm3 density, min. 99.7% purity) were obtained from Merck and were used as received. Double-distilled water was utilized for the formulations.
Deci, deocamdata, import Serbia. Pe plus, performantele s-au imbunatatit:
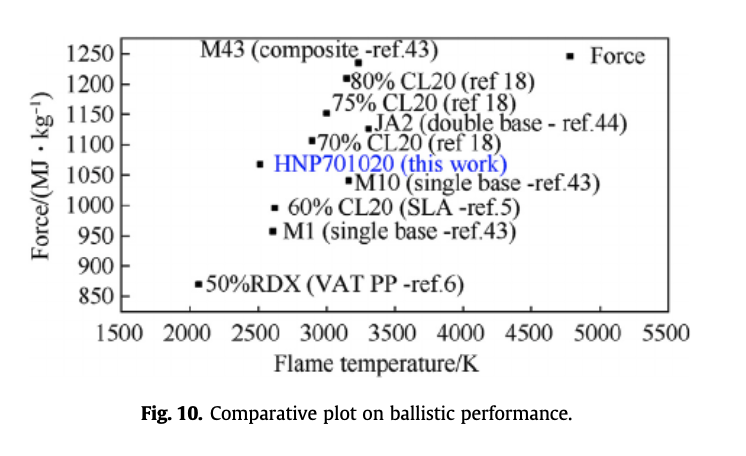
Poate avem noroc si lucrurile vor continua sa evolueze.
Mult mai aproape de intrarea in productie este proiectul “Combustibil compozit cu impact redus asupra mediului pentru sisteme propulsive nedirijate“:
Între sistemele propulsive comune precum cele nedirijate, strict necesare oricărei armate, se numără lansatoarele portabile de grenade, rachete, lansatoare multiple de rachete dispuse pe autovehicule, lansatoare de rachete dispuse pe aeronave și ambarcațiuni. Scopul acestui proiect este acela de a recrea o capabilitate vitală a industriei naționale de apărare, prin transferul dinspre mediul academic și de cercetare, către partenerul industrial C.N. ROMARM S.A. a unei tehnologii inovative de fabricare a unui combustibil compozit pentru motoare rachetă. Dezvoltarea la nivel prototip industrial a acestei noi tehnologii de fabricație a combustibililor de rachetă presupune utilizarea unui oxidant accesibil, cu sensibilitate redusă și cu impact minim asupra mediului, precum și a unor sisteme de lianți energetici ce pot îngloba și materiale obținute prin reciclarea PET. Acești noi propergoli prezintă performanțe cel puțin similare cu cele ale pulberilor cu dublă bază (pe bază de nitrați ai celulozelor și trinitrat de glicerină), în timp ce au o sensibilitate redusă și un impact redus asupra mediului. Combustibilul solid compozit va avea o aplicabilitate duală, putând fi utilizat la nivel național și în cadrul aplicațiilor propulsive civile, dintre care menționăm sistemul național de intervenții în atmosferă cu rachete antigrindină (realizate de ROMARM SA), care la ora actuală utilizează combustibili obsolescenți, poluanți, din import.
Consorțiul din mediul academic și de cercetare care a realizat și validat modelul experimental și care va asista ROMARM SA în dezvoltarea acestei tehnologii este alcătuit din instituții prestigioase cu îndelungată experiență în cercetarea și dezvoltarea de tehnică militară și materiale avansate: Academia Tehnică Militară Ferdinand I, Centru de Cercetare-Inovare pentru Apărare CBRN și Ecologie și Institutul Național de Cercetare – Dezvoltare pentru Chimie și Petrochimie.
Obiectivul general al acestui proiect a constat în transferul către piață al rezultatelor obținute în mediul academic cât și în cel de cercetare, în scopul creșterii competitivității mediului economic.
Astfel, Academia Tehnică Militară „Ferdinand I” (P1-ATM), Centrul de Cercetare și Inovare pentru Apărare CBRN și Ecologie (P2- CCIACBRNE) și Institutul Național de Cercetare – Dezvoltare pentru Chimie și Petrochimie (P3-ICECHIM) au derulat cu succes un proiect intitulat “Compozite polimerice inteligente pentru noi generații de combustibili de rachete – RAKETCOMB”, destinat realizării și validării unui model experimental de combustibil de racheta solid ecologic pe baza de azotat de amoniu stabilizat în faza cristalină, aluminiu micronic, nano-oxizi, lianți și plastifianți energetici de ultima generație, lianți obținuți din PET (polietilen tereftalat) reciclat. În acest context, obiectivul principal al proiectului E-CORA constă în a dezvolta și a transfera la nivel de prototip industrial, tehnologia inovatoare de fabricare a combustibilului compozit solid pentru motoare rachetă către coordonatorul de proiect industrial, C.N. ROMARM S.A.
Descrierea proiectului poate fi gasita de asemenea la sfarsitul postarii.
Mai intai, un rant: cand nu poti produce mai nimic, sa te apuci sa cauti combustibil “cu impact redus asupra mediului“, e ca si cand ai recruta-o pe Greta in fortele pentru operatiuni speciale. Dar probabil ca doar asa se pot obtine fonduri de cercetare deci te faci frate cu Greta pana treci puntea.
Daca in cazul pulberilor de azvarlire se incerca inlocuirea NC/NG, in cazul combustibililor racheta compoziti, bataia pestelui este inlocuirea AP, considerat responsabil de incalzirea globala, topirea ghetarilor, moartea pinguinilor, etc… Si cui nu-i plac pinguinii?
Problema e ca atunci cand inlocuiesti AP cu AN, performantele scad drastic, aducand combustibilul compozit la nivelul (scazut) al combustibililor omogeni dubla-baza. Cu cuvintele lor:
Noua tehnologie presupune utilizarea unui oxidant accesibil, cu sensibilitate redusă și cu impact minim asupra mediului, precum și a unor sisteme de lianți energetici ce pot îngloba și materiale obținute prin reciclarea PET. Acești propergoli prezintă performanțe cel puțin similare cu cele ale pulberilor cu dublă bază, în timp ce prezintă o sensibilitate redusă și un impact redus asupra mediului.
Avand insa in vedere ca scopul a fost obtinerea unui combustibil pentru “lovituri” nedirijate, mai precis “lansatoarele portabile de grenade, rachete, lansatoare multiple de rachete dispuse pe autovehicule“, adica probabil se refera la AG-7, AG-9, PRND-uri si 122mm, care sa poata fi produs aici si acum (si care sa fie si verde), cu costuri minime, desi fara performantele combustibililor compoziti “adevarati”, proiectul si-a atins obiectivele.
Iar faptul ca este deja transferat ROMARM-ului inseamna ca este aproape de introducerea in fabricatie.
Mai departe, pentru pulberi si combustibili superiori – pentru ca vrem rachete ca afara – vom vedea, tinem aproape.
Referinte:
Rezumat_Etapa_1 Rezumat_Etapa_2 Rezumat_Etapa_3 1-s2.0-S2214914725000637-main Prezentare-pe-scurt-a-proiectului-75-PTE_20.06.2024